随着电子工业科学技术的迅速发展,变频器技术的应用已进入蒸蒸日上的时代,国内低压变频技术的应用由上世纪80年代初几家代理公司销售国外产品,发展到上世纪90年代末几家公司拥有低压变频技术的研发水平和制造能力。在低压变频技术得到广泛应用的同时,高压变频技术的研究和应用也初具规模。成都佳灵公司研发的“直高技术”和制造的高压变频器,更使国内的高压变频技术走到了国际水平的前列。1995年起金堆城钼业公司三十亩地选矿厂就高压变频技术在尾矿输送初级泵站的应用,进行了充分的市场调研和参观学习,鉴于当时高压变频设备的体积大、技术复杂,且价格昂贵,迫使该项目搁浅。时间进入21世纪后,工业用电量的突飞猛进,而且电价一路上涨,尾矿输送中的初级泵站应用高压变频器技术节电降耗已势在必行。
1 尾矿输送工艺流程变化引起电能效率降低
尾矿输送是选矿厂生产工艺流程的最末端,在尾矿输送成本费用的总数中,电能消耗费用占有较大的份额。本文所述的选矿厂其尾矿输送工艺流程要求在尾矿输送系统的初级泵站内,输送泵装配高压电动机。该高压电动机的额定参数为:P=3lOkW,U=6kV,=34A。由于生产条件的限定,初级泵站的运转率几乎是100%,电动机运行时输入电流一般为22A左右,月耗电量16×104kw.h以上。近年来由于该选矿厂生产工艺流程的改变,使得尾矿输送的工艺流程出现了两个途径。一是原有的向上50m输送,经300m管道至二级泵站;二是新设的向下5 m输出经1200m管道至尾矿汇集站。按选矿厂生产设定要求尾矿向下输送率≥85%,尾矿向上输送率≤15%。在这种生产系统中,初级泵站的尾矿输送出现了电能的浪费现象。虽然初级泵站的月耗电量已降至13×1O4kW·h,但是电能效率却大幅下降,即H2×W/P2远小于H×W/P1,式中H表示尾矿输送高度,H2=一5m,H1=50m;P表示电动机输出功率,P2=200 kW,P1=230 kW;W表示尾矿输送量,基本是一个恒定值。如此电能消耗的不合理性,改造初级泵站已成必然。但是通过论证,由于受经费条件和地理位置的限制,初级泵站彻底改造困难比较大,投资费用大。最终,减少初级泵站电能浪费的方法,只有是在保证尾矿输送情况下尽可能地降低电动机的功率消耗。
2 选用高压变频技术是初级泵站最佳改造方案
为了寻求节约电能的最佳方案,对初级泵站的主体设备进行了改造试验。在不改变电动机转速的情况下,用210 kW的电动机替换3lOkW电动机。在试验条件下,初级泵运行的电动机输出功率降低到了135 kW,试验取得了成功,为初级泵站的电气改造奠定了理论基础。但是试验过程中出现了初级泵站启动过程繁琐化,启动时需要利用阀门控制,逐渐实现尾矿的全部输送,启动过程所需要的时间长,无法满足选矿厂生产工艺流程的要求。分析造成这种现象的主要原因是电动机额定容量减少后,电动机的启动转矩也随之下降,无法保证输送泵象原来一样地迅速启动。
如果应用高压变频技术控制原配电动机,即可实现电能效率的最大化,又可以简化启动过程和缩短启动时间。根据输送泵相关参数的关系式和电动机的转速公式
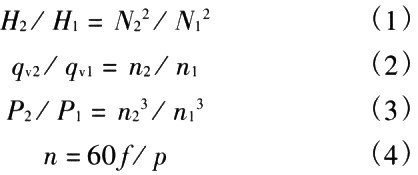
式中:H表示泵的扬程;
qv表示泵的流量;
p表示电动机的功率;
n表示电动机的同步转速。
可以得到电动机在不同频率下运行时与电动机的功率关系式

式(5)说明了电动机运行在较低的频率下,其消耗电能功率会有较大的降低。但是电动机随着输入电源频率的下降,其转速也随着下降。输送泵转速下降后能否保证原系统的工艺流程,也就是说能否保证在流量恒定不变的状态下,实现尾矿顺利输送。从上述实验中得到了系统稳定下电动机的输出功率下降范围在40~80kW。根据式(5)的计算比较,输入电源频率的变化应在30~45Hz范围内确定。再根据式(3)的计算比较,电动机的同步转速应在600~900 r/min的范围内确定。为确保高压变频器技术在初级泵站的应用投资与收益相符合,再次用8极电动机(同步转速750 r/min)在初级泵站进行了工艺流程试验,在其它条件不变的情况下,尾矿稳定输送。试验结果表明电动机在一定范围低转速下运转,输送泵能够保证原生产系统工艺流程。先后两次电力拖动实验取得的数据,坚定了该系统应用高压变频技术能够实现节能降耗的最初设想。
3 高压变频器与尾矿输送设备的匹配设计
初级泵站高压变频器与尾矿输送设备匹配设计的原则依据为:采用“直高”变频器技术,电压等级6 kV;变频设备体积要小,允许占有最大空间2350mm×1200mm×5000mm(高×宽×长);变频设备要求重量轻,厂房结构允许最大承重量4500 kg;变频设备内设电源输入高压真空断路器,距离6kV控制室100m;高压变频器系统控制方式采用开环控制,分7段频率输出与工艺流程相对应实现人机对话控制;高压变频器系统具备多功能的电信号保护和足够的过载能力,保证高压变频系统运行的可靠性和稳定性;设计目标是月节能4×104kW·h.
根据初级泵站环境与工艺流程要求,在遵守设计原则的基础上,通过调研、比较、论证,最终确定了初级泵站应用高压变频器技术的设计方案。最终选用的高压变频设备由4台箱柜组成,总体积2 200mm×1200mm×4970mm(高×宽×长),设备总重量不大于3 500 kg。其中2#变频柜长1 600mm,内装整流桥单元和逆变桥单元;3#系统控制柜长970mm,内装控制电路、保护电路和人机对话显示系统4#低压柜长800mm,内装低压电源支持配电设备;l#开关滤波柜长1 600mm,内装开关单元、电抗器单元、滤波器单元及主变频电路。为了确保尾矿初级泵站在生产月内运转率100%,按全年二次全厂停车检修时间计算,要求高压变频器能够达到连续运行750 h以上,无故障运行4500 h以上。以此确定高压变频器的设计必须达到450 kW,从而保证系统过载能力100%,为实现高压变频系统运行的可靠性和稳定性,在高压变频器控制系统中引入过流、短路、缺相、欠压、过压、接地、过热、过载和电涌共9种功能保护,为防止功率器件在系统异常状态时损坏,设置主器件工作性能保护电路。为最大化的满足初级泵站生产工艺流程控制,在3#控制柜板面设置变频器指令元件,具有启动、停车、频率分段调节和状态指示功能;在3#柜控制柜版面还设置人机对话窗口,主控画面静态显示变频系统当前运行状况,移动画面通过触摸显示变频系统内相关温度和电能参数。
4 安装与调试
从高压变频器技术在初级泵站的实用出发,在市场调研和技术论证基础上,通过对制造费用的资金投人和节电效益的综合分析,高压变频器委托成都佳灵电器制造有限公司生产。高压变频系统设置7段频率分段控制功能,输出频率在5~60 Hz之间任意选择以适应初级泵站工艺流程需要。高压变频器的安装不但要能够满足现场设备运行操作的要求,而且也要充分考虑设备的检修维护和巡视检查的高压电气安全要求。高压变频系统完成实体连接后,进行了系统调试和模拟运行,在凋试过程中解决了方案设计存在的系统控制技术上的缺陷,使频率的分段区间最优化地包含工艺流程可能出现的变化,从而确保高压变频系统运行的稳定性和可靠性,促使电能节约的最大化。高压变频系统投入运行后,通过跟踪检测,数据采集分析结果令人满意。采集的数据如表l所列,而数据经统计后列于表2。由表1和表2可见,该高压变频系统遵循设计原则,实现了设计目标。
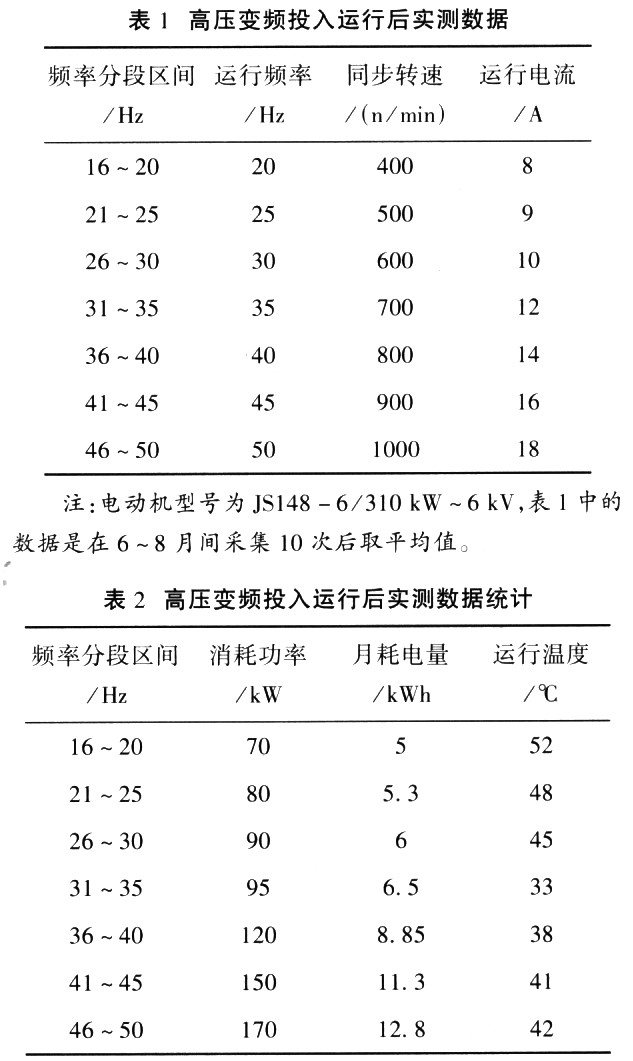
5 结语
高压变频器技术应用于尾矿初级泵站取得成功,高压变频器系统无故障连续运行已达4000h,高压变频设备运行稳定可靠,月节约电能平均达到5×lO4kW·h。
|